Inhaltsverzeichnis
Die Digitalisierung bietet eine Menge neue Chancen und ist eine Grundbedingung für Unternehmen, um zukunftsfähig zu bleiben. In vielen Konzernen und KMU ist die digitale Transformation bereits in vollem Gange. Besonders in Handwerksbetrieben fehlen allerdings häufig Zeit, finanzielle Mittel und technisches Know-how, um sich neben dem herausfordernden Kerngeschäft mit digitalen Lösungen und neuartigen Technologien auseinanderzusetzen. Auf lange Sicht ist das jedoch ein Muss, denn die Digitalisierung wird sich auch im Handwerk durchsetzen. Erfahren Sie, was das für Ihren Betrieb bedeutet und wie Sie von technischen Neuerungen profitieren.
Welche Bedeutung und Vorteile hat die Digitalisierung für Handwerksbetriebe?
Die digitale Transformation zielt nicht darauf ab, bewährte Arbeitsprozesse und traditionelle Arbeitstechniken zu verdrängen oder zu ersetzen. Vielmehr geht es darum, alltägliche administrative Aufgaben zu vereinfachen und dadurch Betriebsabläufe zu optimieren. Das letztendliche Ziel: weniger Aufwand für Verwaltungsaufgaben, mehr Zeit für die handwerkliche Arbeit. Über die Zeit- und somit Kostenersparnis hinaus profitiert Ihr Betrieb jedoch noch von weiteren Chancen: Durch die Verwendung digitaler Technologien präsentiert sich Ihr Betrieb als zeitgemässes, innovatives und aufgeschlossenes Unternehmen.
Allgemein versteht man unter Digitalisierung die Umwandlung analoger Inhalte und Prozesse in digitale Daten. Mithilfe von computergestützten Technologien werden analoge Strukturen in wirtschaftlichen wie auch gesellschaftlichen Bereichen effizienter und zugänglicher gestaltet, zudem ist auf dieser Basis eine Automatisierung von wiederkehrenden Prozessen möglich.
In diesen Bereichen können digitale Lösungen zu einer effizienteren Arbeitsweise beitragen:
- Digitalisierung von administrativen Prozessen wie Angebots- und Rechnungsstellung
- computergestützte Fertigung standardisierter Werkstücke
- Vernetzung mit Zulieferunternehmen für automatisierte Nachbestellung von Rohstoffen oder Ersatzteilen
- Personalverwaltung und Arbeitszeiterfassung über Apps für Mitarbeitende im Aussendienst
- Kontaktakquise durch eigene Website- und Social-Media-Auftritte
- Online-Terminbuchungen für Kundschaft
- Baustellendokumentation mit Apps zum Erfassen von Fotos, Notizen und Fortschritten direkt auf der Baustelle
Chancen und Herausforderungen der Digitalisierung für kleinere und mittelständische Betriebe
Vor allem grosse Produktionsunternehmen sind in der Nutzung digitaler Technologien schon weit vorangeschritten. Im Zuge der „Industrie 4.0“-Bewegung, der sogenannten vierten industriellen Revolution, gehen sie unter anderem mit„Smart Factory“-Konzepten (sich selbst organisierende Produktionsumgebungen) bereits den nächsten Schritt.
Welche Chancen und Bedenken dagegen kleinere und mittelständische Handwerksbetriebe in der digitalen Transformation erkennen, hatten der Zentralverband des Deutschen Handwerks (ZDH) und der Digitalverband Bitkom bereits 2020 in einer Studie zur Digitalisierung des Handwerks herausgefunden. Die Meinungen waren in diesem Erhebungszeitraum noch zweigeteilt:
- 66 Prozent begriffen die digitale Transformation als Chance.
- 56 Prozent nahmen sie als grosse Herausforderung wahr.
- 36 Prozent gaben zu, dass sie Probleme bei der Bewältigung hätten.
Worin im Einzelnen die Chancen und Probleme bestanden (und weiter bestehen), lässt sich aus den detaillierten Studienergebnissen ableiten: Studienergebnissen ableiten:
Chancen der Digitalisierung im Handwerk | Probleme der Digitalisierung im Handwerk |
---|---|
• Zeitersparnis bei Verwaltungsprozessen • Erleichterung bei der Auftragsakquise • verkürzte interne und externe Kommuni-kationswege • verbesserte Konkurrenzfähigkeit durch Angebot neuer Service-Leistungen • automatisierte Funktionsprüfung und Wartung von Maschinen • computergestützte Qualitätskontrollen nach definierten Parametern | • hohe Investitionskosten • überdimensionierte, nicht auf KMUs zugeschnittene Software und Anwendungen • mangelnder Überblick über passende digitale Lösungen • Anforderungen an Datensicherheit und Datenschutz • Berührungsängste aufgrund mangelnder Digitalkompetenz im Team • langsame Internetverbindung in ländlichen Gegenden |
Eine Folgestudie von ZDH und Bitkom aus dem Jahr 2022 stellte fest, dass die Digitalisierung im Handwerk spürbar an Fahrt gewonnen hat. Ein wichtiger Grund dafür war die Corona-Krise, die den Fortbestand von Betrieben gefährdet hatte. Die gestiegene Bedeutung und veränderte Wahrnehmung der Digitalisierung im Handwerk schlug sich dementsprechend in den Umfrageergebnissen nieder:
- 55 Prozent geben an, die Digitalisierung sichere die Existenz ihres Handwerksunternehmens.
- 30 Prozent der Betriebe sind im Zuge der Digitalisierung in der Lage, neue Dienstleistungen anzubieten.
- 83 Prozent der Betriebe stehen der Digitalisierung sehr oder eher aufgeschlossen gegenüber.
Mit dem Fortschreiten der digitalen Transformation geht allerdings auch eine gestiegene Erwartung der Kundschaft einher. So stellen ganze 97 Prozent der teilnehmenden Betriebe fest, dass ihre Kundschaft mittlerweile eine schnelle Rückmeldung erwartet. Im Verbund mit der deutlich erhöhten Preissensibilität, die 77 Prozent der Befragten registrieren, ergeben sich neue Herausforderungen hinsichtlich des Services, der Transparenz und der Erreichbarkeit von Handwerksbetrieben.
Digitalisierung im Handwerk: Voraussetzungen im Betrieb
Gerade in kleineren und mittelständischen Betrieben sind die Mitarbeitenden direkt für den Unternehmenserfolg verantwortlich. Denn anhand von Fähigkeiten, Entscheidungen und Handlungen trägt jedes einzelne Teammitglied nicht nur wesentlich zum erfolgreichen Abschluss von Aufträgen und Projekten bei, sondern in gleichem Mass zur Etablierung neuer Strukturen. Deswegen fällt Arbeitgebenden die Aufgabe zu, die Balance zwischen technologischen Anforderungen, Wirtschaftlichkeit und den Bedürfnissen ihres Teams zu halten.
Es ist unabdingbar, für Transparenz und Aufgeschlossenheit beim Personal zu sorgen, um das Unternehmen erfolgreich an der Digitalisierung teilhaben zu lassen. Denn nur wenn die Mitarbeitenden bereit sind, Neues zu erlernen und anzuwenden, können neue Arbeitsprozesse eingeführt werden. Darüber hinaus müssen entsprechende Arbeitsgeräte, Software und Schulungsmassnahmen zur Verfügung stehen.
Beispiele für die Digitalisierung im Handwerk
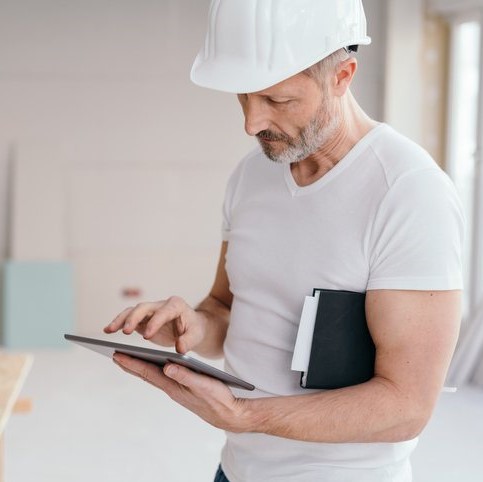
Je nach Betrieb und Branche können ganz unterschiedliche Anwendungen den Arbeitsalltag erleichtern. Folgende Beispiele veranschaulichen, wie digitale Technologien im Handwerk eingesetzt werden können:
- Digitales Bestandsmanagement: Bluetooth-Module an Werkzeugen und mobilen Maschinen melden einer App, wo sich das jeweilige Gerät befindet, und geben Auskunft über Zustand, Wartungsintervalle und anstehende Prüftermine.
- Zeit- und Aufgabenerfassung: Handgeschriebene Stundenzettel werden durch elektronische Dateneingabe und direkte Übermittlung ersetzt. Ein Personalplanungssystem etwa gestaltet nicht nur die Zeiterfassung effizienter, auch Abrechnungen werden automatisiert erstellt und die Schicht- und Urlaubsplanung vereinfacht. Die erfassten Daten sind auch den Mitarbeitenden deutlich leichter zugänglich, was Missverständnisse vermeidet und für mehr Übersicht sowie Transparenz sorgt.
- Abnahmeprotokoll: Stift und Papier waren gestern. An einem digitalen Abnahmeprotokoll können Sie mühelos Anpassungen vornehmen, Ihr Betrieb hinterlässt einen zeitgemässen Eindruck bei der Kundschaft und Sie sparen Materialkosten für Papier, Druck und Aufbewahrung.
- Digitale Archivierung: Es ist nicht nötig, kaufmännische Belege in Papierform aufzubewahren. Praktischer ist es, Belege zu scannen und diese digitalisiert und revisionssicher in einer Cloud abzuspeichern. Ein paar Klicks am Computer ersetzen das Suchen in Papierordnern. Dies schafft zudem mehr Platz in den Betriebsräumen, da weniger Ordner nötig sind.
- Lagerstrategie: Moderne Lagerstrategien und Verfahren wie Pick-by-RFID ermöglichen es beispielsweise, den Lagerbestand vollautomatisch zu überwachen und die Kommissionierung in Echtzeit zu erfassen. Die Verwaltung erfolgt über eine zentrale Software, wodurch menschliche Fehler minimiert werden. Sie haben jederzeit im Blick, welche Artikel sich an welcher Stelle befinden und in welcher Menge sie vorhanden sind. Bei sehr weitläufigen Lagerflächen und der Abwicklung grosser Warenmengen kann insbesondere eine Lagerautomatisierung sinnvoll sein.
- Online-Recruiting: Für Handwerksbetriebe kann die Digitalisierung auch sehr hilfreich sein, wenn sie erfahrene Fachkräfte oder Lernende suchen. Gerade kleinere Unternehmen können mit Online-Ausschreibungen, kurzen Kontaktwegen und moderner Selbstpräsentation im Web ihre überregionale Sichtbarkeit erhöhen, während sie zugleich eine grössere Zahl besser passender Bewerbungen erhalten. Zu einem vollständig digitalisierten Bewerbungsprozess gehören neben Online-Anzeigen auch Tools, die Kommunikation und Auswahl erleichtern.
Förderungsmöglichkeiten für Betriebe
Vielen KMU mangelt es an finanziellen Mitteln, um die Digitalisierung im Handwerk voranzutreiben. Falls auch Sie dazu gehören, können Sie sich zum Beispiel an berufliche Netzwerke oder die kantonale Wirtschaftsförderung wenden.
Der Bund schlägt auf seiner Seite „Unterstützung bei der Digitalisierung der KMU“ unter anderem folgende Organisationen vor:
- „Swissmen / Industrie 2025“: Dieser Dachverband der KMU und Grossunternehmen im Industriebreich fördert die Digitalisierung und Industrie 4.0 mit Massnahmen wie Information, Sensibilisierung und finanzielle Förderung der Schweizer Unternehmen, die die Industrie 4.0 aktiv implementieren.
- „Kantonale Wirtschaftsförderung“: Die Anlaufstellen für Wirtschaftsförderung der verschiedenen Kantone unterteilen Ihnen in Bezug auf die Digitalisierung Auskünfte und bringen Sie mit den zuständigen Personen zusammen. Teilweise bieten die kantonalen Dienste auch Finanzbeihilfen für technologische Innovation an.
FAQ zur Digitalisierung im Handwerk
Mithilfe von computergestützter Automatisierung werden Arbeitsprozesse vereinfacht, optimiert und effizienter gestaltet. Diese wird ergänzend zur menschlichen Fachkenntnis verwendet und soll diese keinesfalls ersetzen.
Die Optimierung von Arbeitsprozessen spart Zeit und Kosten, Menschen können effektiver arbeiten. Zudem ist der Betrieb am Puls der Zeit und präsentiert sich gegenüber Aussenstehenden als innovatives, modernes und aufgeschlossenes Unternehmen.
Die Fachkenntnis der einzelnen Mitarbeitenden ist und bleibt von zentraler Bedeutung. Das handwerkliche Know-how ist eine grundlegende Voraussetzung, um Arbeitsgänge mithilfe digitaler Prozesse zu erleichtern. Denn nur wenn handwerkliches Können vorhanden ist, kann dieses mit zukunftsweisenden Technologien ergänzt werden. Mitarbeitende in Logistik und Handwerk sollten lernbereit sein, Führungskräfte wiederum müssen erforderliche Software und Arbeitsgeräte sowie Schulungsmassnahmen bereitstellen.
Die Organisation Swissmen / Industrie 2025 erteilt Beratung und Zuschüsse für Unternehmen, die an der digitalen Transformation teilhaben wollen. Zudem bieten einige kantonale Anlaufstellen für Wirtschaftsförderung Finanzbeihilfen für technologische Innovationen wie die Digitalisierung an. Bei der zuständigen Handwerkskammer erhalten sie Informationen über lokale Förderprogramme, mit denen die Digitalisierung im Handwerk unterstützt werden soll.
Bildquellen:
© gettyimages.de – Svetikd, Danchooalex, Stockfor